12月22日德阳日报:
国产大飞机C919关键承力构件是经过了哪些过程才得以应用?世界上最大的8万吨模锻压机首位操作手是怎样炼成的?在这背后,是产学研一体化的创新平台通过不断的技术创新、人才培育,从而撑起这些大国重器的脊梁。
走进四川工程职业技术学院四川省航空材料检测与模锻工艺技术工程实验室,工作人员正在认真地进行材料检测。随着金属材料样本件工作温度的升高。正进行着持久蠕变实验。
“这个实验室用于检测某-材料,在某一个工作温度下受恒定载荷作用时,抵抗斯裂和允许的塑性变形的极限能力。作为高温构件设计选材的重要依据,以保证设备安全。以航空材料为例,提供数百到数万小时的数据。“该实验室副主任李艳丽介绍道,实验室围绕材料检测技术研究、材料塑性变形及其数值模拟等开展研究,为开发模锻生产工艺提供有力的技术基础支撑.通过产学研一体化培养人才模式,为重装制造业提供技术开发、检测服务和人才培训等服务,实验室重点支持成德绵周边的航空航天企业的材料检测,并致力于培养时代高端技术人才,也是中国航空工业等检测人员培训基地。
该实验室还曾为大国重器的研究研发贡献出“科技创新力量”。在实验室里,正在忙碌的专职研究人员吴代建对记者讲述了一个大国重器背后的故事:“国产某型飞机钛合金承力框锻造成形过程中,出现了局部成形不足折叠等技术难题.严重影响产品交付和装机保障。实验室对接企业.安排研究人员开展项目技术攻关。经过夜以继日地研发。无数次的试验.形成了具有独立知识产权的专利技术,并经生产验证后,得到了推广应用。”
不仅如此,该实验室及项目依托学校产学研平台,坚持“产教融合校企合作”的育人方针,培养了大批以8万吨模锻压机首位操作手叶林伟为代表的中央企业青年岗位能手和技能大师,解决了“世界之最,谁来操作的难题,为以C919大飞机为代表的航空锻件制造贡献着中国特色高水平高职学校的中坚力量。
据了解,近年来,四川工程职业技术学院搭建的产学研平台,与北京航材院中国二重.德国KUKA等合作,共建了航空材料检测、工业机器人等4个四川省工程实验室和德阳(西广]子)高端装备智能制造创新中心、德阳科技成果转移转化中心等平台,牵头成立“四川省装备制造业产教联盟”,努力为高喘装备智能制造提供高技能人才和技术服务支撑。
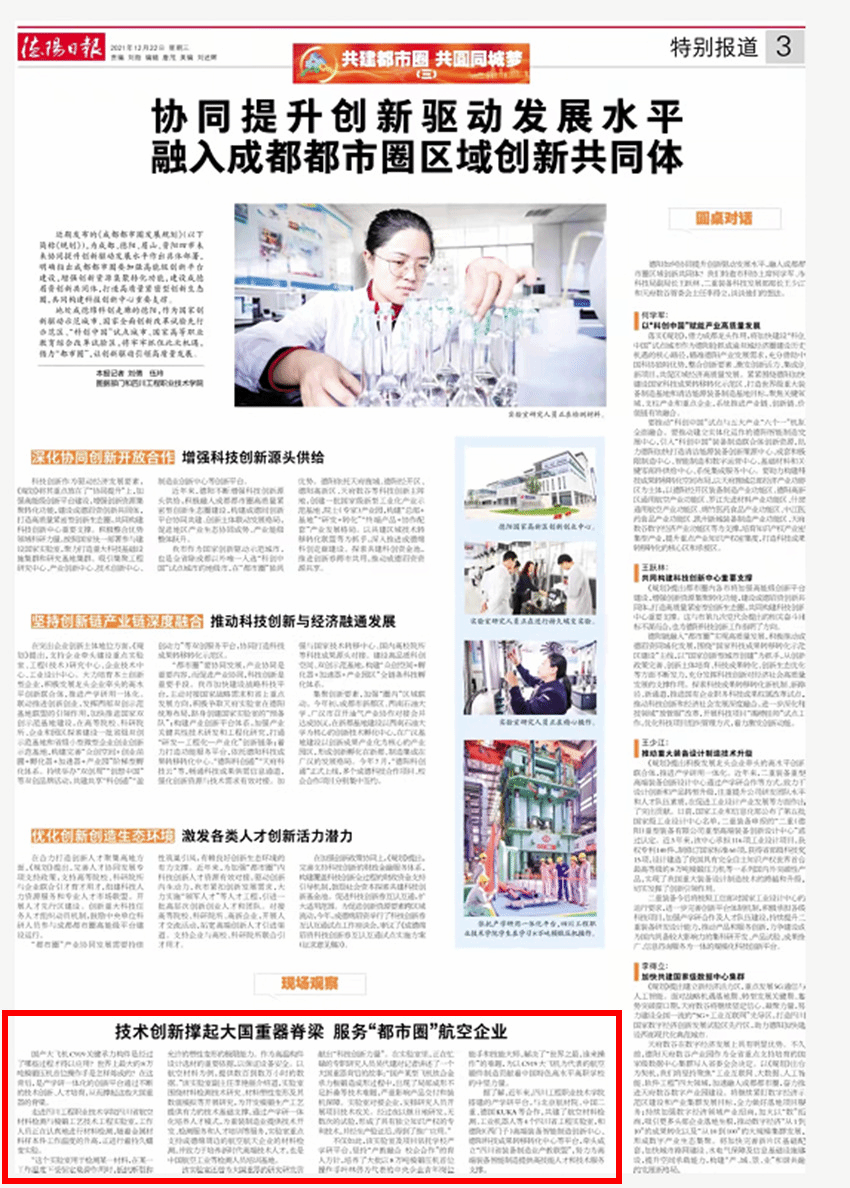